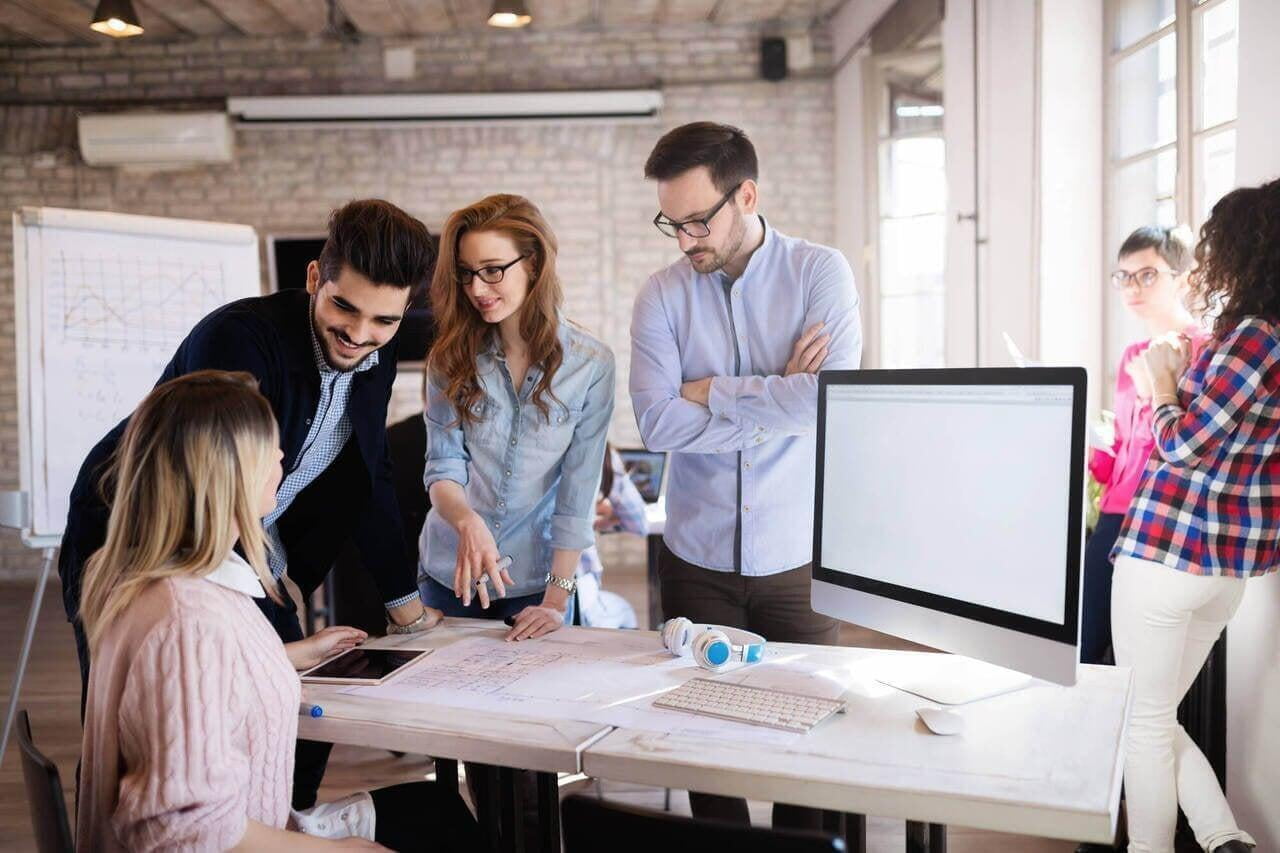
Historically, companies have avoided significant changes in their operations, but today change is an inevitable part of the economy. The increasing globalization has led to companies asserting themselves in global competition, and with the modern emphasis on change, many companies use change management consulting to optimize transitions. Let’s examine further what change management entails.
Business Growth
Organizations that excel in change management, especially in business start-ups, can achieve a number of objectives: promote growth, increase shareholder returns, and drive innovation.
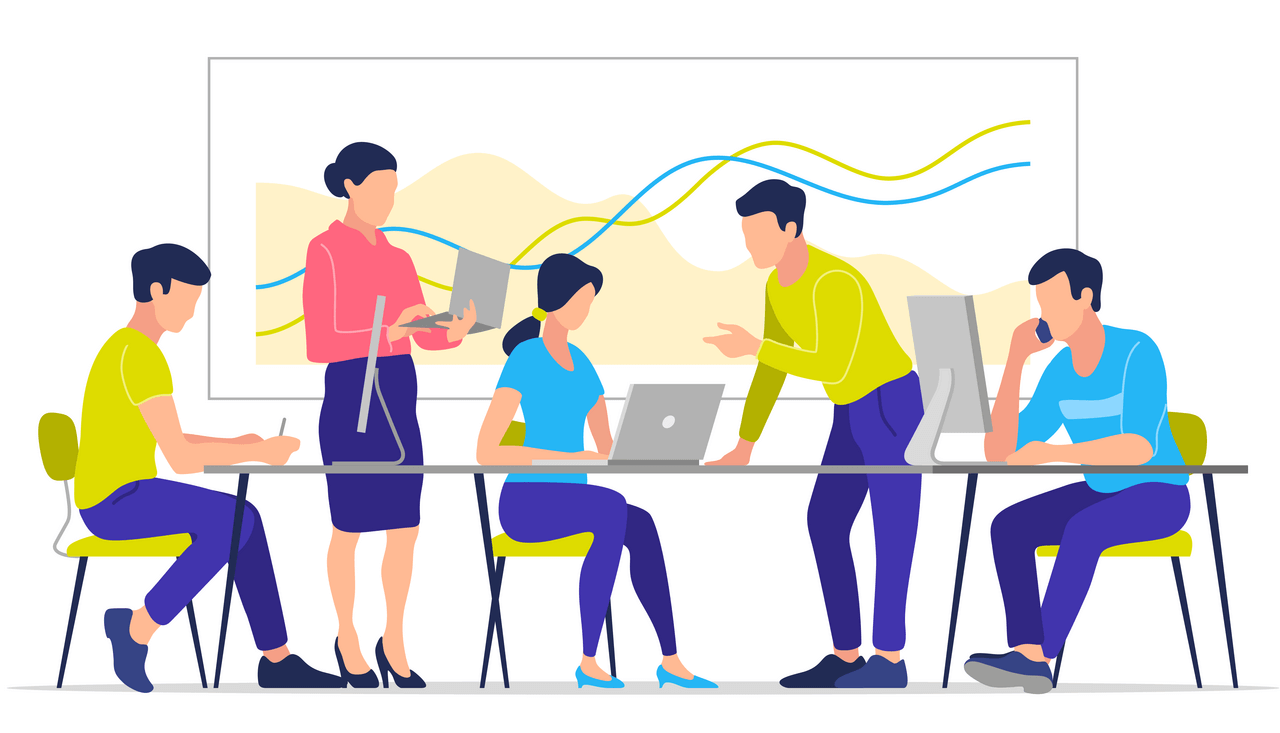
Adaptability
Adaptability gives you a clear competitive advantage, but equally important is the ability to reinvent yourself and strengthen your capabilities when new opportunities and challenges arise.
Stakeholder Involvement
At the heart of meaningful change are the people who are involved. Change management consultants can help companies by bringing stakeholders on board and keeping them informed. Stakeholder involvement can also help to improve the effectiveness of information exchange on change and increase stakeholder participation and support. By engaging and communicating effectively with people who are not being sold for change, consultants provide feedback, and leaders can move faster toward higher goals. If you stay consistent and use your advisers correctly, you will reinforce the key messages of change.
Effective Strategies
By implementing training programs and effective strategies and providing the necessary equipment, organizations create the infrastructure to accept change and create a culture around their work. To implement far-reaching changes, consultants work with organizations to help change or even completely deconstruct their organizational norms.
Developing A Change Management Plan
Too often, companies fail to set targets that are either too narrow or structurally disorganized. By outlining the desired outcomes of organizational change, goals can be communicated to all stakeholders so that they are able to understand and connect the benefits and goals of their organization. Operations consultants can work with management to develop fiscally appropriate targets while being optimistic about the company’s growth potential.
Before change can be implemented, goals and outcomes must be defined, and change management is based on several key components that serve to achieve these goals. Key components include developing a change management plan, engaging stakeholders, developing a vision, engaging leaders, creating supportive infrastructure, and adequately measuring progress.
The first step is to assess the current capacity for change within the organization to assess its readiness for change. This allows management consultants to act as an alternative to the opposing managers and the employees themselves. If staff feel there is no clear commitment from the manager, they lose confidence in proposed changes. To achieve these goals, companies should work with a change management consultant to create a clear change management plan. If a company wants to significantly change how it operates, it must take steps to ensure that the process is productive.
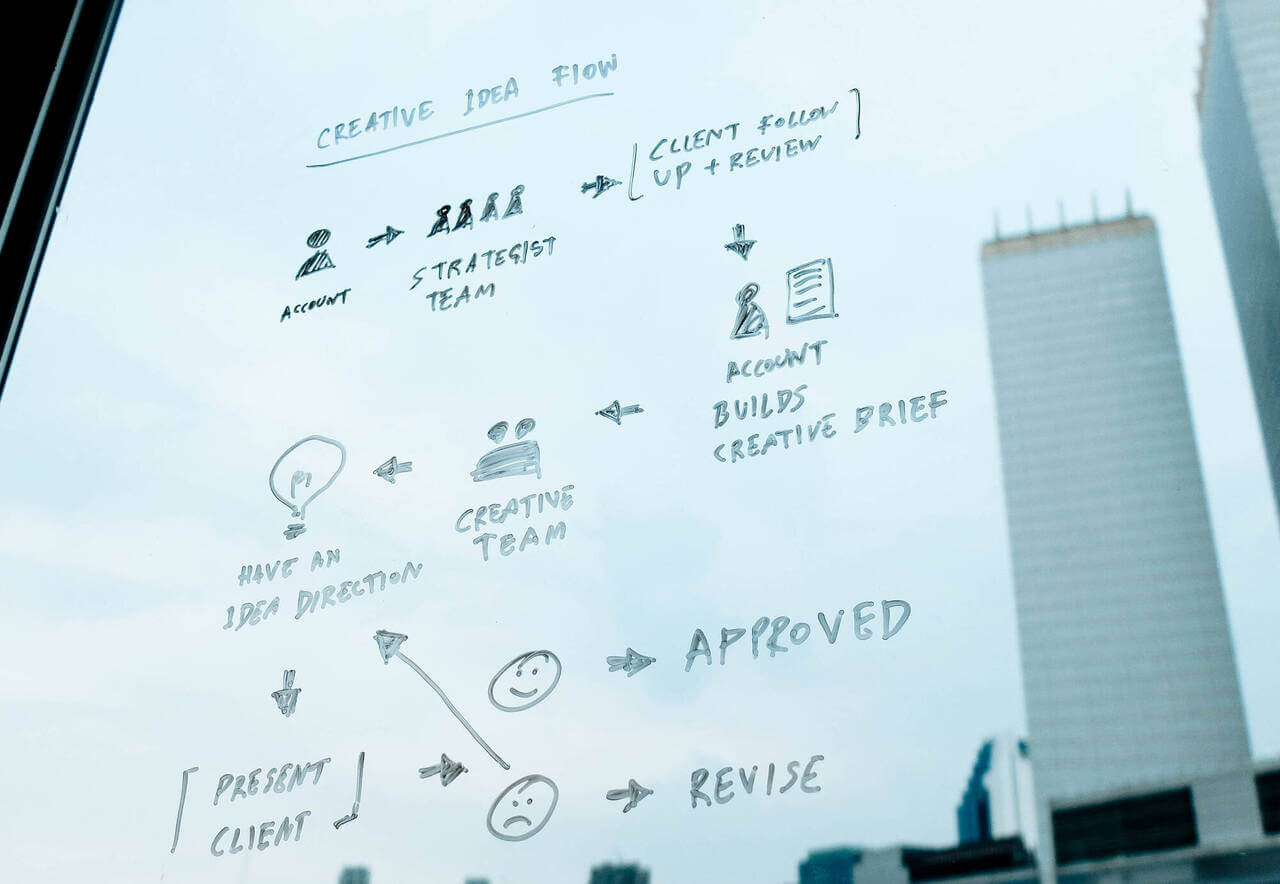
Implementing Changes
The resulting plan should cover all aspects of the effort, including implementation, post-implementation, and institutionalization. Consultants and managers can then use the Change Management Plan to inform and decide whether changes should be implemented once or in phases. This is followed by a risk analysis to identify potential obstacles that could hamper the implementation of changes. As part of the change management process, change management consultants take a well-thought-out approach in the process that leads to changes in the environment of the organization to help effectively implement change.
Preparing for Change
Management consultants know that change does not happen all at once, and one of the key factors in motivating stakeholders is to emphasize the potential benefits and growth that come from change because, without this information, stakeholders would be reluctant to move. To implement changes effectively, consultants can ensure a smooth transition by preparing to achieve high growth targets.
Before moving, both consultants and executives should understand the need for change and prepare to move away from current activities. One of the most effective methods for change is to gather your champions of change (individuals who naturally take the lead and are open to adapting) and inform them of the upcoming adjustments. They can help you set the tone throughout your organization and will be key in shifting from one model to another.
Applying Changes
The next step focuses on the movement that takes place within an organization in response to change. The initial phase tends to be difficult because many people are initially uncertain about change, and without sufficient time and support to understand the agents of change, they risk losing sight of the overall vision. Rather, it is the reaction that the process can provoke along the way, not the change itself, but the reactions of those involved to the changes.
The change management process also involves having the difficult conversations that are necessary to bring about change, building on the conversations you have had and knowing where your organization is going, and ensuring that you achieve those conversations by implementing effective and powerful change management strategies. A change management consultant helps to ensure that the most important goals of change are constantly communicated, and that appropriate training is offered.
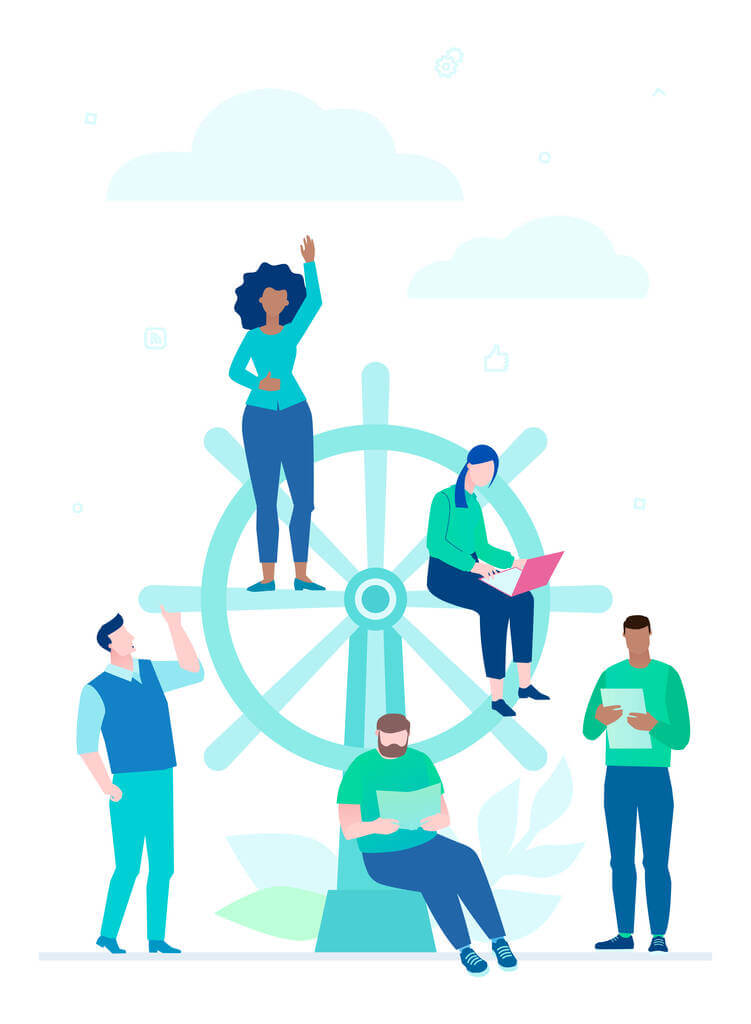
Monitoring Changes
When changes occur, consultants should monitor the data in real-time and ensure that the desired results are achieved. You can learn about unique situations in real-time, receive support and acquire new knowledge and skills when you work with a consultant. The aim of this phase is to cement change in the overall culture and prevent regression into the behavior of the past. When people accept change, they feel comfortable with the new routine.
The last stage is designed to provide stability before changes are implemented, allowing the company to expand and grow better. Once changes are implemented, consultants should continuously monitor progress, but the work of change management consultants does not end with implementation. Identifying and tracking the best indicators to assess progress allows consultants and managers to make adjustments where necessary. Measuring data can also give companies insight into the impact of change and its impact on the long-term success of the business.
Lean Six Sigma for Change Management
Lean Six Sigma for Change Management
One thing that helps in finding leadership support is to be able to explain what Lean Six Sigma is and why it makes such a difference. Let us understand one of the most important aspects of Lean Six Sigma, the principles of quality management.
What Is Lean Six Sigma?
What Is Lean Six Sigma?
Lean Six Sigma is a system to analyze and improve processes, services, and products. We know the process can be difficult for clients to understand. That’s why we’re committed to providing training, resources, and continual support throughout the Lean Six Sigma process. Lean Six Sigma is a powerful tool for change management. It is a systems approach to improvement that emphasizes the importance of reducing waste, reducing variability, and increasing efficiency in a business or organization. It's made up of several different methodologies, all driven by real data through the use of data science, data engineering, and data analysis.
Lean Six Sigma is an organization-wide approach to process improvement that seeks to maximize the value produced for our customers while minimizing waste. It helps us analyze where problems might be in existing processes and propose solutions to these issues. To improve business processes, it uses a collection of statistical and management methods that helps companies identify and eliminate waste within business processes so that consumers receive higher quality products and services at lower cost.
Understanding The Principles of Lean Six Sigma
Understanding The Principles of Lean Six Sigma
A successful Lean Six Sigma project places a strong focus on employee engagement and a clear strategy for change management. Lean Six Sigma allows staff members to make improvements by utilizing data that is collected during specific tasks and projects. It is a method that has become the basis for innovation in corporate culture, and reviewers must be part of the problem - both the solution process and the change process. By introducing the Lean Six Sigma principles, you can change the mindset of your employees and managers towards a mindset focused on growth, continuous improvement, and process optimization.
Six Sigma training focuses on deviations from target performance, but is recursive, which facilitates waste identification and disposal. Waste in Lean Six Sigma is everything that does not add value to the end product or meet customer expectations. Lean Six Sigma training focuses on waste, and there is a strong correlation between the use of this method and the success of the program as a whole. But it can be misused, undermining the expected organizational benefits of such an initiative.
Benefits of Lean Six Sigma
Benefits of Lean Six Sigma
The ability to effectively manage a Lean Six Sigma project shows that the organization is ready to take on more responsibility. Facilitating the change process effectively will undeniably lead to more commitment and continued support from the management team and your employees. Lean Six Sigma is also in itself a change management tool that will facilitate the necessary changes. When managers see Lean Six Sigma as a value system for the processes of the organization, they can tackle obstacles and challenges more effectively. This requires an external approach to business processes, which is at the core of Lean Six Sigma.
Adopting The Lean Six Sigma Method
Adopting The Lean Six Sigma Method
Companies and organizations are therefore seeking to implement Lean Six Sigma as part of their long-term strategy to manage change. Modern companies, therefore, prefer the Lean Six Sigma approach, which is driven by the need for companies to change and continuously improve their workflows. Organizations that pursue quality initiatives within the company now choose lean six sigma as the basis for their business model and processes.
Other organizations are striving to be in business with a long-term approach to continuous improvement by trying the Lean Six Sigma method and testing its variations. If you choose this method and follow its principles, you can optimize your process once and for all. Adopt the principles of Lean Six Sigma and promote a culture of responsibility and ownership within your organization.
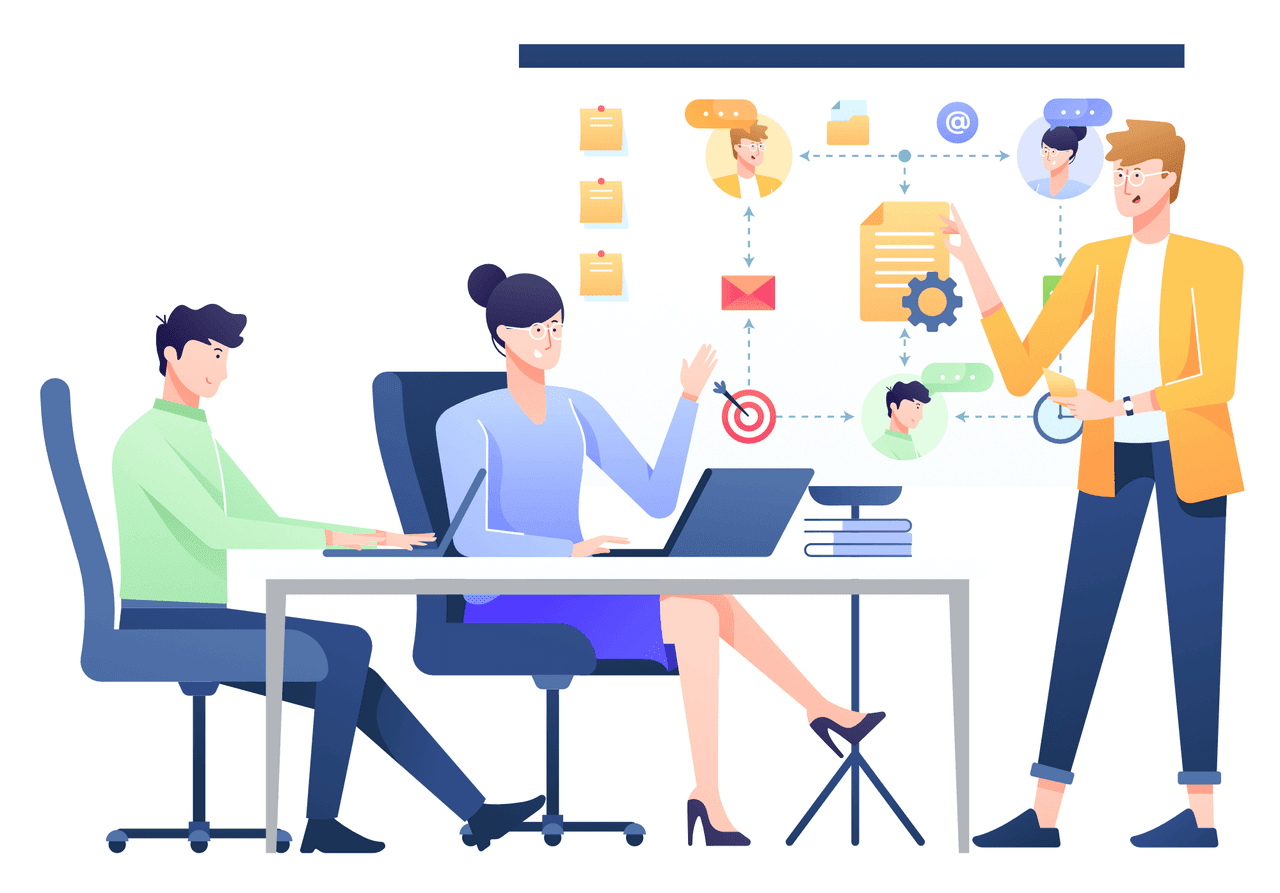
Change Management Consulting
Change Management Consulting
More than half of organizational change projects fail to meet their targets in large transformation programs. Our consulting services help clients increase these projects’ success rates and outperform competitors with new opportunities. Many companies still need to master the art of organizational change, but to avoid stumbling blocks, we help companies design their change management strategies. Our operations consulting services work with consultants to facilitate the transition of organizations from one business unit to another or from one new organization to another to ensure that the reorganization of an organization runs smoothly for the teams and individuals involved. We help organizations complete their change management plan for the next phase of their business.
Contact us if you need more information on how our team of experts can help you develop your change management plan. Operations consulting can help companies to ensure an effective and efficient transition. Change management consultants understand that change must begin with the leaders of the organization. Therefore, consultants work directly with managers to implement change initiatives to increase the likelihood of achieving the desired results.